In today’s fast-paced business world, supply chain management (SCM) is more than just a back-end operation. It’s a strategic powerhouse that drives profitability, enhances customer satisfaction, and creates a competitive edge.
At its core, SCM is about managing the flow of goods, information, and finances from the initial sourcing of raw materials to the delivery of the final product to the customer. But to truly master SCM, businesses must embrace comprehensive strategies and best practices that optimize every step of the process.
In this article, we’ll explore key strategies, from effective sourcing and procurement to leveraging technology and sustainability practices. We’ll also provide real-world examples to show how these strategies translate into success.
- What is supply chain management?
- The 5 Key components of an effective supply chain
- How to create strategic planning in supply chain management?
- Risk management in supply chain operations
- Leveraging technology and automation in supply chain management
- How to incorporate sustainability in supply chain?
- Optimizing supply chain performance
- What are the benefits of optimizing supply chain management?
- Driving success through strategic supply chain management
What is supply chain management?
Supply chain management is the coordination and management of a network of interconnected businesses involved in providing goods and services to end-users. This process encompasses everything from sourcing raw materials to delivering finished products.
Effective SCM aligns these components with the overall business goals, ensuring that every part of the chain operates cohesively. When done right, SCM can lead to significant cost savings, improved efficiency, and enhanced customer satisfaction.
The 5 Key components of an effective supply chain
To build a successful supply chain, optimizing each component is essential. Here’s how:
1. Planning
Effective planning serves as the foundation for a streamlined supply chain. It involves forecasting demand, coordinating production schedules, and aligning all supply chain activities to minimize disruptions.
Steps to enhance planning:
- Leverage data-driven forecasting. Use historical data and predictive analytics to forecast demand accurately. This helps you align production schedules with customer demand, reducing the risk of overproduction or stockouts.
- Coordinate with stakeholders. Ensure close collaboration between departments like procurement, production, and logistics. Integrated planning across the supply chain can reduce delays and inefficiencies.
- Implement contingency plans. Prepare for potential disruptions by developing contingency strategies for issues like supplier delays, natural disasters, or sudden demand changes. Flexibility is key to maintaining a resilient supply chain.
2. Sourcing and procurement
Sourcing and procurement are the backbone of your supply chain. These involve identifying reliable suppliers, negotiating terms, and acquiring the materials necessary for production.
Best practices:
- Develop strong supplier relationships. Trust and reliability are critical. Building long-term partnerships with suppliers can lead to better terms, priority access to materials, and more effective problem-solving.
- Focus on cost-effective sourcing. It’s not just about finding the cheapest materials but about balancing cost with quality and reliability. This helps prevent supply chain disruptions due to poor-quality materials or unreliable suppliers.
- Prevent shortages. Proactively manage your supply levels to avoid production halts. Use predictive analytics to forecast demand and adjust orders accordingly.
3. Inventory management
Efficient inventory management helps you meet customer demand without tying up too much capital in unsold goods.
Strategies for success:
- Optimize inventory levels. Strive for a balance that meets customer demand without overstocking. This reduces waste and improves cash flow.
- Reduce inefficiencies. Identify and eliminate bottlenecks in your supply chain that cause delays or excess costs. This could involve anything from streamlining warehouse operations to refining order processing.
- Maintain a smooth flow of goods. Ensure that products move seamlessly from suppliers to warehouses to customers. Implement real-time tracking systems to improve supply chain visibility and address issues as they arise.
4. Warehousing and distribution
The final step in the supply chain is getting the product to the customer. Effective warehousing and distribution make this happen quickly and cost-effectively.
Key considerations:
- Efficient warehousing. Organize your warehouse for maximum efficiency. Use automated systems to manage inventory and reduce human error.
- Streamline distribution. Work with reliable distributors and logistics providers to ensure timely delivery. Consider factors like route optimization and last-mile delivery options to enhance performance.
- Enhance supply chain performance. Constantly evaluate and refine your distribution processes. Use metrics like delivery times and order accuracy to measure success and identify areas for improvement.
5. Reverse logistics
Reverse logistics refers to the process of moving goods from the customer back to the business for returns, repairs, recycling, or disposal. An efficient reverse logistics system can enhance customer satisfaction and reduce waste.
Key strategies for reverse logistics:
- Simplify the returns process. Create a streamlined and user-friendly process for customers to return products. The easier it is for customers, the faster the return process can be completed, minimizing delays in handling.
- Recapture value from returned goods. Evaluate returned products to determine if they can be refurbished, reused, or recycled. This can help reduce waste and recover value from returned items, contributing to sustainability goals.
- Enhance tracking and visibility. Implement a robust tracking system for returned products. This ensures that you can monitor the status of returns, repairs, or recycling processes, optimizing reverse logistics efficiency.
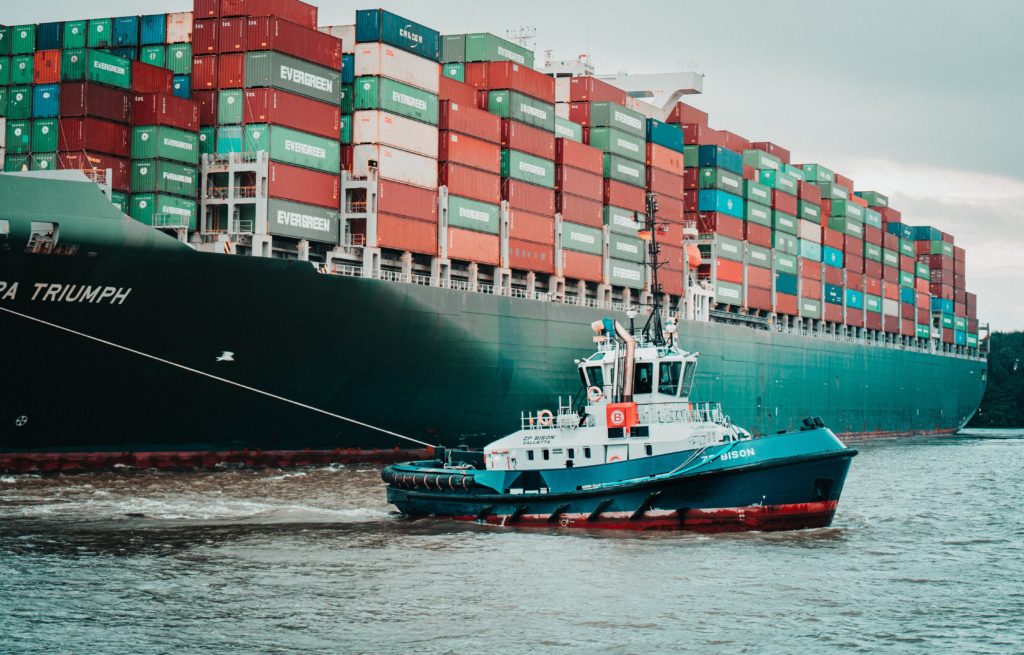
How to create strategic planning in supply chain management?
Strategic planning is at the heart of effective supply chain management. It involves setting long-term goals and developing a roadmap to achieve them.
Creating an effective supply chain strategy:
Align with business goals
Your supply chain strategy should directly support your overall business objectives. Whether reducing costs, entering new markets, or improving customer satisfaction, your SCM strategy should be in lockstep with these goals.
Steps to align with business goals:
- Understand the big picture. Regularly engage with leadership to understand the company’s strategic direction. Is your business focusing on global expansion? Are you prioritizing cost-cutting measures? Your supply chain strategy should reflect these priorities.
- Customize supply chain KPIs. Use key performance indicators (KPIs) that directly measure the supply chain’s contribution to business goals. For example, if the goal is improving customer satisfaction, focus on metrics like on-time delivery rates and order accuracy.
- Adapt to changing goals. As your business evolves, so should your supply chain strategy. Regularly reassess your supply chain’s alignment with business goals, making necessary adjustments to ensure continuous support for your company’s objectives.
Forecasting and predictive analytics
Use data-driven insights to anticipate demand and adjust your supply chain accordingly. This helps prevent both shortages and excess inventory, leading to better financial outcomes.
Best practices for forecasting and predictive analytics:
- Use historical data for better predictions. Leverage past sales data, seasonal trends, and customer purchasing patterns to forecast future demand more accurately. This helps maintain optimal inventory levels, preventing shortages or overstocking.
- Incorporate real-time data. Use real-time data from various sources, such as market trends and social media, to adjust your supply chain in real-time. This can help you respond quickly to unexpected changes in demand.
- Automate the forecasting process. Implement AI-driven predictive analytics tools to automate and enhance forecasting accuracy. These tools can analyze vast amounts of data and predict trends, giving you a competitive edge in managing inventory and meeting customer demand.
- Scenario planning. Use predictive analytics to run “what-if” scenarios, allowing you to prepare for different market conditions. This could include simulating the impact of supply chain disruptions, sudden demand spikes, or changes in supplier reliability.
Aligning supply chain activities
Ensure that every part of your supply chain is working toward the same goals. This includes everything from procurement to distribution, as well as your relationships with suppliers and logistics providers.
Strategies for aligning supply chain activities:
- Collaborative planning. Encourage cross-functional collaboration between teams involved in sourcing, production, inventory management, and distribution. Hold regular meetings to ensure all departments are working toward the same goals and resolve any misalignments.
- Supplier and logistics alignment. Ensure your external partners—suppliers, logistics providers, and distributors—are aligned with your business objectives. Communicate your goals clearly and regularly review their performance to ensure they are supporting your supply chain strategy.
- Integrated technology. Use integrated supply chain management software to align activities across the entire supply chain. This provides a centralized view of operations, helping to eliminate silos and improve coordination between departments.
- Continuous improvement. Regularly review and optimize processes to improve alignment. Use performance metrics to assess whether all aspects of the supply chain are contributing to overall efficiency and meeting business goals.
By taking a proactive approach to SCM, you can anticipate challenges before they arise and turn your supply chain into a competitive advantage.
Risk management in supply chain operations
Risk management is a critical component of supply chain operations. With global supply chains becoming increasingly complex, the potential for supply chain disruptions has grown. Supply chain leaders must be prepared to address risks that could impact the flow of goods, from natural disasters to geopolitical issues.
Key strategies:
- Diversify suppliers. Relying on a single supplier can be risky. By diversifying your supplier base, you reduce the chances of a single disruption causing significant delays.
- Develop contingency plans. Have backup plans in place for critical parts of your supply chain. This could include alternative routes, backup suppliers, or emergency inventory.
- Involve stakeholders. Engage all relevant stakeholders in risk management discussions. Their insights can be invaluable in identifying potential risks and developing strategies to mitigate them.
Effective risk management can help your supply chain remain resilient in the face of unexpected challenges, protecting your business from costly disruptions.
Leveraging technology and automation in supply chain management
Technology is a game-changer in the modern business landscape for supply chain management. Automation and advanced analytics can streamline processes, reduce costs, and improve decision-making.
Technological advancements in SCM:
- Automation. Automating repetitive tasks like order processing or inventory management can free up time and reduce errors. This leads to a more efficient supply chain and better use of resources.
- ERP systems. Implementing an ERP (Enterprise Resource Planning) system can integrate all aspects of your supply chain, providing a single source of truth for your operations. This enhances visibility and ensures that all parts of the supply chain are aligned.
- Real-time data and analytics. Use real-time data to monitor your supply chain in action. This allows for quick adjustments and more informed decision-making. For example, if a shipment is delayed, you can reroute it to prevent a stockout.
- Operational efficiency. New technologies like artificial intelligence and machine learning can optimize everything from forecasting to inventory management.
- Cost reduction. By using predictive analytics, businesses can minimize waste and reduce costs, ultimately improving profitability.
How to incorporate sustainability in supply chain?
Sustainability isn’t just a trendy buzzword – it’s a necessity for modern supply chains. Companies are increasingly being held accountable for their environmental impact, and sustainable practices can also lead to cost savings and improved brand reputation.
Incorporating sustainability into SCM includes:
- Green supply chain practices. Implement eco-friendly practices at every stage of your supply chain, from sourcing raw materials to delivering the final product. This could involve using renewable energy in production processes, reducing waste, or optimizing transportation routes to cut emissions.
- Reducing environmental impact. Focus on minimizing the negative environmental impact your supply chain has. This includes reducing carbon footprints, minimizing waste, and sourcing materials sustainably.
- Balancing cost-effectiveness with sustainability. While sustainability initiatives sometimes involve upfront costs, they often lead to long-term savings. For example, using energy-efficient processes can reduce utility bills, and reducing waste can lower disposal costs.
By embracing sustainability, businesses can reduce their environmental impact, enhance their reputation, and meet the growing demand for eco-friendly products.
Optimizing supply chain performance
Optimization is a process of continuous improvement, focusing on refining every aspect of your supply chain. By regularly assessing and fine-tuning your operations, you can increase efficiency, lower costs, and drive overall performance improvements.
Here’s how to optimize supply chain performance:
Leverage technology for automation and data analysis
Modern technology plays a crucial role in optimizing supply chains. Implement supply chain management (SCM) software to automate routine tasks, such as order processing, inventory tracking, and demand forecasting.
These tools can provide real-time data, helping you make informed decisions and spot inefficiencies quickly. Use data analytics to gain insights into trends and patterns, which can guide inventory levels, sourcing strategies, and logistics decisions.
Example: A company could use predictive analytics to forecast demand and optimize inventory, ensuring that products are in stock without over-committing resources to excessive inventory levels.
Implement lean methodologies
Adopt lean principles to eliminate waste in your supply chain. This involves identifying bottlenecks, reducing excess inventory, and streamlining processes to ensure a smoother flow of goods.
Regularly review each step of your supply chain to determine where unnecessary delays or costs are occurring and work on removing or reducing these inefficiencies.
Example: Assess your transportation and logistics operations to optimize routes and reduce fuel costs, delivery times, and emissions.
Foster supplier collaboration
Optimizing supply chain performance isn’t just about internal processes—your suppliers play a key role as well.
Collaborate closely with your suppliers to share forecasts, demand data, and production plans. This can lead to better alignment, reduced lead times, and more responsive supply chains.
Example: Partner with key suppliers on joint improvement initiatives, such as better production scheduling or developing more efficient delivery processes.
Optimize inventory levels
Holding too much inventory ties up capital, while too little inventory can lead to stockouts and missed sales.
Use demand forecasting tools and just-in-time (JIT) inventory practices to maintain the right balance. JIT practices minimize storage costs while ensuring that products are available exactly when needed.
Example: Implement inventory management systems that automatically reorder stock when levels fall below a certain threshold, based on real-time data.
Improve logistics and distribution
Optimizing logistics is a significant part of supply chain performance. Consider integrating route optimization tools to reduce delivery times, fuel costs, and shipping errors.
Additionally, focus on enhancing last-mile delivery, as this is often the most expensive and time-consuming part of the logistics process.
Example: Analyze your distribution network to see if it’s more efficient to consolidate shipments, use regional distribution centers, or partner with third-party logistics providers.
Invest in workforce training and development
Your team is central to supply chain performance. Regularly train employees on new technologies, best practices, and lean processes. When your workforce is skilled and knowledgeable, they’re more capable of identifying and addressing inefficiencies before they impact overall performance.
Offer continuous training programs on the latest supply chain management tools or conduct workshops focused on lean principles.
What are the benefits of optimizing your supply chain management?
Optimizing your supply chain offers a range of tangible benefits that impact not just your operations but your overall business success. A well-optimized supply chain creates a ripple effect, improving everything from cost efficiency to customer relationships.
By continuously refining and improving your processes, you position your company for long-term success and sustainability.
Key benefits of supply chain optimization:
- Improved customer satisfaction. A finely tuned supply chain ensures that customers receive their orders accurately and on time. This reliability not only enhances customer satisfaction but also builds trust and loyalty. When customers know they can count on you to deliver, it leads to repeat business and positive word-of-mouth.
- Competitive advantage. In today’s fast-paced market, being able to deliver products faster, at lower costs, or with higher quality gives you a significant edge over competitors. By consistently optimizing your supply chain, you can stay ahead of the competition and respond quickly to market changes or customer demands.
- Cost efficiency and profitability. Optimization leads to streamlined processes, reduced waste, and lower operational costs. By identifying inefficiencies and eliminating unnecessary steps, you can reduce overhead, minimize delays, and lower the cost of goods sold. This directly contributes to improved profit margins.
- Better supplier relationships. Supply chain optimization often involves close collaboration with suppliers. By developing stronger relationships and ensuring smooth operations, you can benefit from better terms, more reliable deliveries, and improved communication. This mutual partnership can lead to long-term cost savings and enhanced operational efficiency.
- Greater visibility and control. With optimized systems in place, you gain better visibility into every stage of your supply chain. This increased transparency allows for more accurate tracking, faster decision-making, and greater control over the entire process. You can easily identify issues as they arise and address them proactively.
- Environmental sustainability. Optimizing your supply chain often leads to reduced waste, energy consumption, and emissions. This not only lowers operational costs but also aligns your business with environmental sustainability initiatives. As more consumers prioritize eco-friendly brands, a green supply chain can also boost your company’s reputation.
- Improved decision-making through data. Supply chain optimization often goes hand in hand with better data collection and analytics. With improved access to data, you can make more informed, strategic decisions that impact both the short-term and long-term success of your business.
Driving success through strategic supply chain management
Supply chain management is more than just a logistical necessity – it’s a strategic tool that can drive success and growth. By implementing comprehensive strategies and best practices, businesses can optimize their supply chains to achieve cost savings, improve efficiency, and gain a competitive advantage.
Key takeaways:
- Strategic planning is crucial. A well-thought-out supply chain strategy that aligns with business goals is key to success.
- Technology is a game-changer. Leveraging technology and automation can significantly improve supply chain performance and decision-making.
- Sustainability matters. Incorporating sustainable practices into your supply chain can lead to cost savings and enhance your brand’s reputation.
At IMD, we believe in empowering leaders with the tools and knowledge they need to master supply chain management. Our programs are designed to provide participants with the skills and strategies necessary to drive success in their organizations.
Explore how IMD’s global supply chain management programs can help you optimize your supply chain and achieve your business goals. Join us on a learning journey that will transform your approach to SCM and set you up for long-term success.
Get the latest management content in your inbox 💌