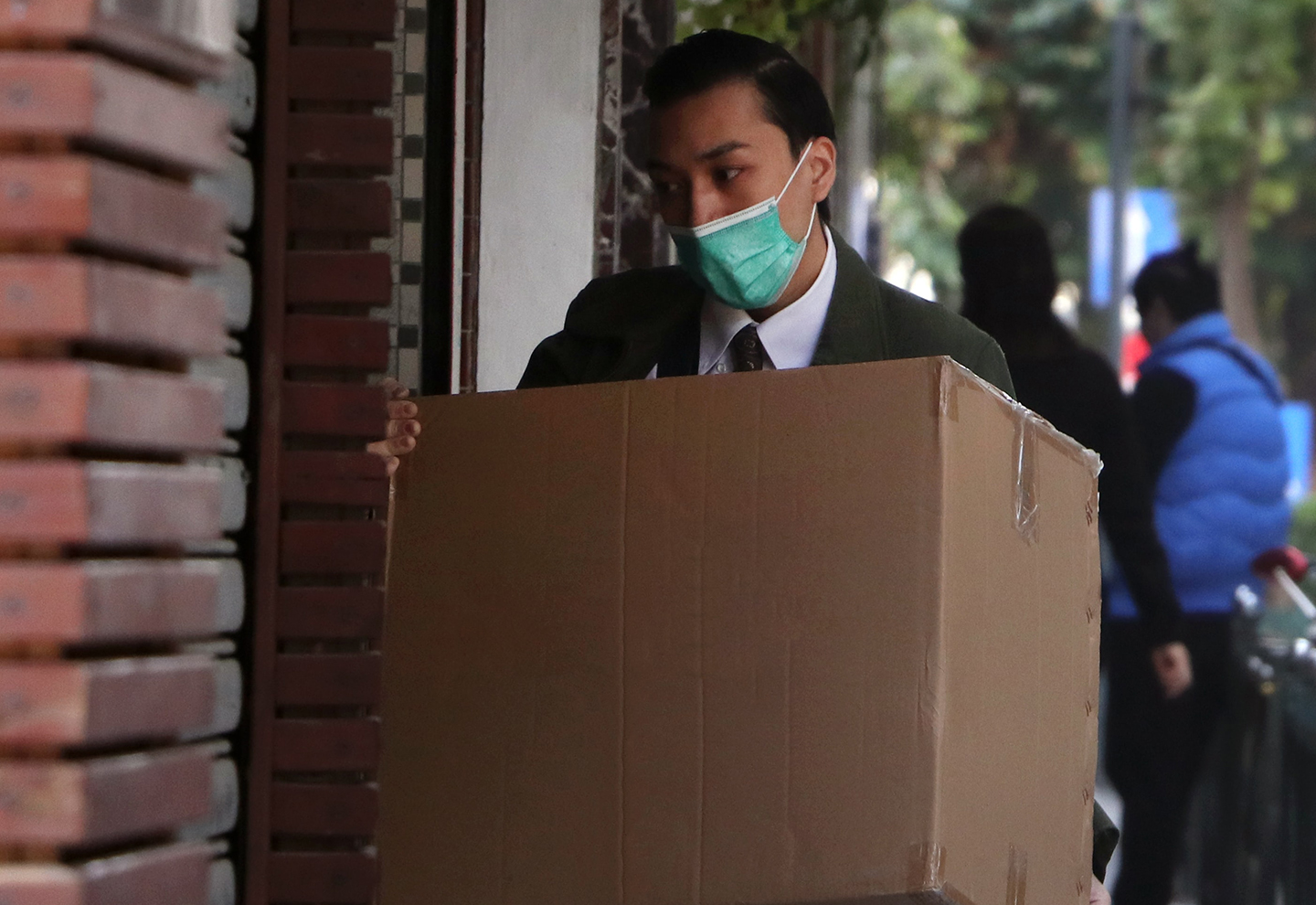
Digesting the shocks: how supply chains are adapting to the COVID-19 lockdowns
As the world grapples with the human and economic crisis unravelling before us, supply chains are finding themselves squarely within the public eye and experiencing unique challenges of their own.
First, the supply shocks
For weeks at the start of the year, as COVID-19 was taking its toll on China, experts were focusing on ‘supply shocks’. These were disruptions to the availability of goods sourced from China; both finished goods for sale and products used in factories in developed markets. Companies scrambled to sort out what production was feasible, and what demand could be met.
At that moment, it made sense to think of supply chain resilience. We have previously talked about the lessons learned on resilience for global value chains under threat and the five supply chain resilience levers companies should put in place.
Some companies will already have integrated these learnings while others, in the interests of costs, and at the sacrifice of agility and resilience, have been relentlessly consolidating production and extending sourcing.
Second, the demand shocks
As the pandemic crisis deepened and nations have begun instituting lockdowns, supply chains have been experiencing something completely new: systemic demand shocks, where people are stocking up on consumer staples in order to comply with restrictions on movements, in some cases buying months’ worth of goods in a single day.
The most talked-about example, toilet paper, is ironically usually the go-to example of a perfectly forecastable product, since the end consumption is usually rather stable. There seemed to be a fear that food supply chains would be unable to respond to this unprecedented, massive spike in demand.
With a few exceptions, consumer staple supply chains have answered the call. Store shelves have been restocked and this has provided a measure of reassurance to people in a distressing time. But the supply chain professionals behind the scenes have accomplished this with a herculean exceptional effort, as the classic planning models are not built to accommodate such severe peaks in demand.
The replenishment models that dictate orders from retail chain distribution centers to stores can be notoriously manual and lacking in sophistication. They are best suited to continuous, relatively smooth demands. With pipelines being emptied out, there was a scramble to redirect inventories, identify priorities and override IT supply proposals.
On the production side, the successful replenishment is the result of maximizing production with all spare capacity in use. Since food supply chains are usually finely tuned for steady demands, the full pipeline has likely not yet been restored.
The resilience issue is less relevant for food supply chains as they tend to be much more local than non-food supply chains.
Third, the aftershocks
Many readers will have heard of the bullwhip effect. It describes the way in which demand spikes tend to amplify as they move up the chain. A small increase in demand at the consumer level may lead to a large increase in production at a food manufacturer or their packaging suppliers. So, it is fair to ask: Will the bullwhip strike now?
There are reasons to think it will not. Among the key drivers of the bullwhip effect is a lack of visibility into the nature of the demand increase. One imagines that all actors in the supply chain are very well aware of why demand is increasing, and that it does not represent an organic evolution in the sales of the product.
However, there is one classic cause of the bullwhip effect that must be managed, and that is ‘shortage gaming’. This describes how, when there is a shortage of a product, the tendency is for downstream actors to inflate their supply needs artificially, in order to claim a greater share of a scare resource.
This will require vigilance moving forward to be sure that visibility into true supply priorities is not lost as pipelines are refilled.
The supply chain has not seen the end of manual interventions in supply processes, however. Many replenishment systems use simple moving averages to calculate store-level requirements. With such an unprecedented demand spike polluting these moving averages, supply chain planners will have to modify supply quantities manually and scramble to adjust their planning systems.
Adding to the complexity moving forward is the ability to develop robust demand plans. There are several variables that bring unique uncertainty. It is impossible to predict how consumers will behave moving forward, since the extent and duration of restricted movements is unknowable.
Will demand return to a normal baseline, or will there be waves of large-scale buying? It is also challenging to know to what extent restaurant closures will have a clear impact on the level of grocery purchases.
Fourth, the new normal
The economic impacts are beginning to be felt, and many economists are predicting a deep recession of unknown length. Indeed, while some supply chains are spinning incredibly hard to keep up, others such as VW in automotive are being forced to ramp down.
For supply chain planners, one pitfall to avoid in order to move forward is the dynamic called the inventory bounce. When demand reaches a new steady state that is lower than the previous steady state, there must be a cut in production to allow the pipeline of stock to lower to a new steady state level. At that point, production actually increases a bit to match the new demand.
In the last major recession ten years ago, the inventory bounce fooled some upstream supply chains into thinking that demand was rebounding. The bullwhip effect kicked in and the bounce became amplified. Havoc and distress prevailed.
Out of the shocks, an opportunity?
The shrinking of the supply chain footprint dynamic may accelerate as companies seek a different cost/resilience trade-off and look to localize production and sourcing.
Now has also been a moment for the supply chain to step up and contribute. One company resolved a shortage of parts for life-saving ventilators in Italy by using 3D printing and making them available within a day (though they are being sued for their efforts). Perhaps this trigger the creation of a role for additive manufacturing in the spare parts supply chain.
LVMH, L’Oréal and Coty and others have stepped up and repurposed production facilities intended for fragrances and hair gels in order to produce hand sanitizer. In addition to providing a valuable resource that may help save lives, this move helps keep workers on and facilities operating despite difficult economic conditions for luxury items.
A unique moment
Supply chains are showcasing singular resourcefulness and adaptability, though the challenges are far from over. But the outcome may be fundamental changes and a whole host of managers and regulators who find it second-nature to rethink global models and supply dependencies.
Ralf W. Seifert is Professor of Operations Management at IMD. He directs IMD’s Digital Supply Chain Management program, which addresses both traditional supply chain strategy and implementation issues as well as digitalization trends and new technologies.
Richard Markoff is a supply chain researcher, consultant, coach and lecturer. He has worked in supply chain for L’Oréal for 22 years, in Canada, the US and France, spanning the entire value chain from manufacturing to customer collaboration. He is also o-founder and Operating Partner of the Venture Capital firm Innovobot.
Research Information & Knowledge Hub for additional information on IMD publications
The supply chain risk management literature differentiates between disruption risk that arises from supply disruptions to normal activities and recurrent risk that arises from problems in coordinating supply and demand in the absence of disruption...
Supply chain management experts Ralf Seifert and Richard Markoff pose the question: is fulfilment still an FMCG core competency?
As society moves further into the digital age, emerging technologies bring unprecedented opportunities for economic growth, operational efficiency and societal advances. Emerging technologies such as artificial intelligence (AI), quantum computing...
Research Information & Knowledge Hub for additional information on IMD publications
Research Information & Knowledge Hub for additional information on IMD publications
Research Information & Knowledge Hub for additional information on IMD publications
Research Information & Knowledge Hub for additional information on IMD publications
Research Information & Knowledge Hub for additional information on IMD publications
in Production and Operations Management 16 November 2024, ePub before print, https://doi.org/10.1177/10591478241302735
Research Information & Knowledge Hub for additional information on IMD publications
Research Information & Knowledge Hub for additional information on IMD publications
Research Information & Knowledge Hub for additional information on IMD publications
World Economic Forum White Paper, October 2024
Research Information & Knowledge Hub for additional information on IMD publications
in I by IMD
Research Information & Knowledge Hub for additional information on IMD publications